|
|
 |
 |
|
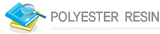 |
|
 |
|
 |
What is Unsaturated Polyester? |
|
Polyester is a polymer melt which must contain one component of unsaturated acid such as maleic anhydride or formic acid which is further combined with saturated poly-basic acid, a type of phthalic anhydride, and esterified with polyhydric alcohol such as propylene glycol or ethylene glycol which produces unsaturated alkyd and finally this is dissolved in stylene monomer(SM) or other types of polymerization monomer. |
|
 |
Types of Unsaturated Polyester |
|
1) Raw Material |
Ortho-phtalic acid, Isophthalic acid, Bisphenol, Vinyl-ester, Novolac, Halogenation, etc |
2) Usage |
General type, soft type, weathering resistance, corrosion, thermal endurance, non-combustible, low elongation resin |
3) Casting |
For FRP, molding, coating, SMC, BMC, gel-coating, button, special, etc. |
|
 |
Definition and Charateristics of Unsaturated Polyester |
|
1) Acidity |
To find out the esterization reaction rate. The amount of potassium hydroxide(§·) required to neutralize Carboxyl Group contained in a gram of resin.
Resin normally contains 20-50 acid value and the reaction worsens as the resin increases.
|
2) Viscosity |
Molecular weight of unsaturated-alkyd and softening point. It is influenced by the quantity of distilled SM and the measurement of viscosity is poise(PS).
Types are produced according to the weather. (autumn, summer, winter) To lower the viscosity level, use SM at a degree lower than 5%.
|
3) Humidity |
0.02%-0.2% may be contained in packed products. However, when moist is increased during the manufacturing process or from other factors, hardening or other properties decreases.
|
4) Thixotropy |
Controled with eruzil to prevent streaming when lining & coating vertically. |
5) Sclerotic Contraction |
When the resin hardens it causes 7 -10% of volume shrinking.
Increases according with the quantity of SM resins.
When SM content is above 30%, it is hard to expect shrinkage below 5%.
Considering the shrinkage, the size should be made larger than the product when producing basic MOLDs.
|
|
 |
Technical & Chemical Characteristics of Resin - (Tested with KSM3305) |
|
1) Tensile Strength |
The load at the point when the material breaks by pulling each side divided by the material¡¯s cross section. |
2) Compressive Strength |
The load at when the material breaks by gradually adding force divided by the material¡¯s cross section. |
3) Bending Strength |
Calculated at the point when the material breaks by adding force to its center (material should be leveled to the ground).
|
4) Elongation |
The gauge length measured after the material breaks by adding force to each end. |
5) Corrosion |
The increase in weight and appearance when the material is heated at a specific temperature in a specific chemical for a specific amount of time. |
6) Weathering resistance |
When resins are exposed to ultraviolet rays for a long time, they become active and turn yellow. To prevent this a ultraviolet ray absorbent is added (fluoro resin, fluoro film) |
7) Heat resistance |
Test by placing the material inside a thermostat for a certain period and observe its appearance or measure the heat deflection temperature.
General Resin¡¦below 100¡É
Iso Resin¡¦100-120¡É
Novolac Resin¡¦130-160¡É
|
|
 |
WAX |
|
1) Resin is divided into two categories-WAX and NON-WAX type.
2) The side contacting with air needs to be coated with wax to achieve full hardening (For General Laminate Resin).
3) Gel coat, being a NON-WAX type stacks up well. When adding WAX to NON-WAX types 2% of WAX should be added to 1% of the main material.
|
|
 |
Accelerator |
|
The sudden mixture of accelerators and hardeners result to severe reactions. Thus, it is necessary to store and use these items separately. Accelerators shall be mixed to the main material at least before 12-48 hours and the composition mixing should take place at least before 5 hours.
Precipitation occurs due to the evaporation of SM when melting cobalt, FIFO is requested. DMA is sometimes used in the winter.
|
|
 |
Hardener (MEKPO) |
|
The main element of hardeners is alcohol which volatilizes and water is generated. Therefore, first in, first out is necessary.
Hardeners should be stored in a place with no heat and light. Hardeners should be stored in glass material such as stainless and PE, and iron materials or compound metals should be avoided. Furthermore, Hardeners may explode against impact.
|
¨ç MEKPO- Achromatic Liquid- For room temperature hardeners (for general use) |
¨è BPO-Powder-Mesophilic hardeners (80-120¡É), heat hardeners |
¨é TBPB- Achromatic Liquid-High Temperature hardeners |
|
|
|
|
|
|
 |
|
|
|  |
|
|
|